There is no better feeling than overtaking a competitor in the esses only to have that feeling quickly become a pit-in-the-stomach sensation as the brake pedal drops closer to the floor than usual while braking into the next high-speed corner. For some reason, the pads have been pushed away from the rotor’s surface. Now, the pedal must travel further because the initial pedal application merely presses the pads back into contact with the rotor.
The braking system pressure has not increased to the point of forcefully applying the pads against the rotors and slowing the vehicle. This delay in stopping application gives quite a scare, but it also results in the car leaving the optimum racing line traveling deeper into a corner than expected. Missing the racing line causes a late return to the throttle, and unfortunately, because of this time lag, the competitor previously passed, quickly motors by your wayward vehicle. This scenario was likely a result of pad knockback. To find out how to eliminate knockback, we contacted Rick Elam of Baer Brakes Systems for his insights.
Above: Baer Brakes delivers detail-oriented performance brake kits for the muscle car era and late-model Mopars. If modifications or machining are necessary for the factory spindle, Baer handles all of it for you, so when the Baer kit arrives, it is ready to install.
Above Left: As a vehicle travels in a straight line, the brake pads and rotor are parallel with one another (or should be). The pistons and piston seals of the caliper maintain the pads near the rotor. Above Right: When lateral forces from cornering are induced, pad knockback can occur. Rotor runout or component flex causes knockback, which pushes the pistons back through the piston seals and into its caliper bore when the brakes are released. When the brakes are applied at the next corner, the brake pedal will drop closer to the floor as the pistons must travel a greater distance before the brake system pressure begins to build up.
So, what is knockback? As a vehicle travels down a street in a straight line, the brake pads and rotor are parallel (or should be) with each other, if the brakes and suspension are in proper operating order. The pistons and piston seals of the caliper maintain the pads near the rotor. When the brake pedal is applied, there is a rapid pressure build-up in the braking system because the pads are in contact with the rotor. However, if the vehicle is thrown into high-speed turns, lateral loads are created in the chassis. These turns cause deflections of the tires, wheels, hubs, bearings, and spindles (and additional chassis components). Although the parts seem solid, not one of them on any vehicle is 100% rigid.
This movement (flexing) of the components causes the rotor to lose its parallelism with the pads. The pads are forced back, which slightly pushes the pistons further into the caliper seals. Thus, the initial brake pedal application will not immediately increase the brake system pressure; instead, it takes up the pad knockback distance before the system pressure increases. Elam stated, “In regards to brake or pad knockback, the biggest thing to know is that it’s not the brakes! The brakes themselves do not cause knockback. When knockback occurs, it’s the brakes telling you there is an issue elsewhere.”
Above Left: Many of the 70s Mopars came equipped from the factory with floating front calipers. The floating design allows the caliper to move on an anchor plate without making metal-to-metal contact with it. The calipers are supported by bushings and O-rings that slide on guide pins and sleeves. Above Right: Floating calipers work well on daily drivers. They tend to have a single inboard piston, which reduces the chances of fluid leaks. The design is compact so that a small diameter wheel will fit over the caliper. But the floating calipers tend to flex or twist under extreme braking situations, which contributes to knockback and a soft pedal. The reduced mass of the caliper (compared to a fixed caliper) will not dissipate heat as effectively.
Above Left: If you, or someone you know, has an A-body Mopar, chances are the drum brakes have been swapped to a ’73-’76 sliding caliper design. The caliper body moves on an anchor plate, and it makes metal-to-metal contact with it. Sliding calipers move on machined ways and are retained by unique keys. Above Right: The sliding calipers have the same advantages and disadvantages of the floating calipers. The floating and sliding calipers must have their pins or ways kept free of debris; otherwise, a seized caliper may result, resulting in a caliper that is unable to apply or release.
Is knockback something that should be a concern in a street-driven Mopar? The answer is almost 100% no because the chassis will not be worked hard enough to cause component flex. Many original Equipment Manufacturer (OEM) applications utilize a fixed bracket with a floating (or sliding) caliper. Advantages of floating/sliding calipers are the compact design, with usually a single-piston, which reduces the chances of leaks.
Still, the disadvantages, such as caliper flex and slow heat transfer to the anchor plate and other suspension components, limit it to street only use. For increased street performance and the weekend warrior applications, Baer recommends a fixed caliper with a floating bracket. The fixed caliper allows for pistons on both sides of the rotor, and the floating bracket reduces the flex concerns.
With more powerful cars and wider, stickier tires, concerns arise with flexing the front spindles and causing knockback. Elam stated, “Stock pin-style spindles can have a lot of flex when somebody is putting a sticky 300-series tire on and going around a corner as fast as they can.” Elam has witnessed racers experiencing knockback while utilizing pin-style spindles. Because of this, most serious racers are crossing over to a bearing pack spindle that’s much stronger and significantly reduces knockback.
Above Left: Baer Brakes has designed their front brake kits to work with the factory disc or drum spindles. All that is necessary is to select (online) the spindle design of your vehicle or contact the Baer reps with all the vitals of your ride, and Baer will reengineer (as necessary) spindles to fit your application. Above Right: With increased performance demands, the factory parts could extend into a situation of component flex. Baer can extensively modify the factory spindle or fabricate a completely new spindle assembly for your vehicle. Although this spindle is not a factory Mopar part, it is apparent that Baer constructs high-quality components for all applications.
The rear disc brakes are subjected to the same lateral forces as the front brakes. The production solid rear ends in older Mopars are a semi-floating design, which means that the axle shafts support the vehicle weight and provide the driveline torque to the drive wheels. There are two types of axle shaft retention. The first type is the C-clip rear ends, such as a 7 ¼- or 8 ¼-inch design. These will have some axle movement known as end play.
While in the axle housing when under load (increases with pinion shaft wear), and there is some flex in the axle between the outer bearing (pressed into the axle housing) and the axle hub. The second type is the non-C-clip rear ends, which includes the 8 ¾-inch, Dana 60, and the Ford 9-inch rear ends. This design has the outer bearing and retainer pressed onto the end of the axle shaft. This design may have less end play, but the axle still sticks out between the bearing and the hub, and that distance results in flex.
Above Left: The floater snout is bolted to the axle housing, and the snout supports the backing plate and caliper mounting brackets. The hub rides on bearings between the snout and the hub. The drive axle is splined to the differential and, on the opposite end, to the hub drive. Above Center: If you plan on hitting the track regularly, converting to a full-floating rear end will virtually eliminate pad knockback concerns. The full-floating rear end supports the vehicle weight, so the axle shaft is only responsible for applying the differential torque to the drive hub. Above Right: With the full floater assembled. Each component can be viewed in its installed position. The Baer Brakes kits are even compatible with late-model ABS systems.
“If the car is going to see anything other than casual cruising, Baer recommends at least a Ford 9-inch (Mopar 8 ¾ and Dana 60) style semi-floating rear,” disclosed Elam. Baer has found with the increases in horsepower over the last twenty years, and with the combination of wider wheels wrapped with stickier tires, the 9-inch style rear end with a minimal 1- to 2-inch axle stick out has a minor amount of flex and thus reduced pad knockback. Elam noted, “How Baer solves knockback is to use a full floater rear. For one, this eliminates 100% of any pad knockback, but it’s a safety issue as well, where if the axle fails (breaks), you can still roll and stop instead of losing a wheel.”
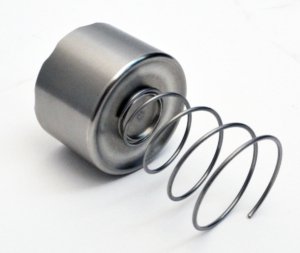
What makes a full-floating rear end better in conditions with high lateral forces? The brake hub rides on two tapered bearings, which distributes the load over a larger area. The weight of the vehicle is transferred through the wheel to the spinning hub and directly to the axle housing via the two bearings. Each axle is splined on both ends, and they “float” between the carrier assembly and the hub. The axle shaft provides the engine torque but is not responsible for bearing the vehicle’s weight.
All the brake system components are attached to the axle housing, and, as the car experiences lateral loading, the brake surfaces remain in alignment with each other. A full-floating design is more costly, mainly due to the labor required to modify the housing, but recently, there have been “bolt-on” designs introduced, which have reduced the costs significantly.
Could there be “cheaper” alternatives to reduce knockback without bolstering the front suspension and switching to a full-floating rear end? Some prefer the use of active piston springs to help control knockback. These are springs placed behind the caliper pistons that push the piston outward to help maintain pad-to-rotor contact.
Elam stated, “In very select applications we use them, but generally speaking these don’t fix pad knockback. If the spring is strong enough to keep the piston engaged and the pad against the rotor, you will have a massive drag in the brakes.” How about the use of residual pressure check valves? “We don’t use or recommend them either. These (hold) only a few pounds of pressure, which isn’t enough to fully cure pad knockback. If they held enough, then you’d have drag issues in the brakes,” explained Elam.
Above Left: Depending upon your performance desires and the spindles on your vehicle (factory drum or disc), Baer has a complete front disc kit for you. This 11-inch SS4+ Brake System features 4-piston calipers, two-piece slotted, drilled, and vented zinc plated rotors. The calipers are DOT compliant. The hubs are pre-assembled and ready to install. All the mounting brackets, brake hoses, and hardware are included. This fixed caliper design is an excellent improvement over the factory parts, yet it will fit neatly inside a 15-inch factory wheel. Above Right: On the other end of the spectrum is the 14-inch (or 15-inch) Front Extreme+ Brake System. This system utilizes a six-piston fixed caliper and slotted, cross-drilled, vented zinc plated rotors. The rotors come with stainless hardware. The hubs are a billet construction, and they come fully assembled with premium bearings. The 14-inch rotors will fit most 18-inch or larger wheels while the 15-inch rotors will clear 19-inch or larger wheels.
Even after reducing or eliminating any flex in the spindle and axle assemblies, there will still be a small runout due to bearing endplay. But even with this limited endplay, each driver will have a difference in opinion about what is acceptable. “You could have two identical cars, but one has a bigger tolerance. One driver will think it is a perfectly fine feeling, while the next driver will hate it. There’s no set number of what is acceptable as it depends on the car, the driver, and the driving situation,” stated Elam.
Some drivers have developed a technique of tapping the brake pedal with their left foot before entering a corner. The quick tap takes up any pad knockback clearances and ensures there is a firm pedal when braking is necessary.
If you have a Mopar that sees some autocross, road course track time or spirited street driving, take the time to provide the Baer Brakes’ representatives with your vehicle’s vital information. The representatives can recommend a complete braking system, which includes calipers, rotors, master cylinder, and pedal ratio options to meet your needs. Moving from factory parts to a Baer setup will guarantee you have confidence in your brakes, and you will keep your competition in the rearview mirror.